The United Nations developed 17 Sustainable Development Goals (SDGs) as part of the 2030 Agenda for Sustainable Development in the assault of a series of problem seen globally. The problems—ranging from ending poverty and improving health, to improving education and economic growth, aim to be tackled while fighting climate change.
When looking at climate change, one significant contributor to global emissions is the logistics industry. According to reports, the transport and logistics sector accounts to about a quarter (24%) of all global carbon emissions.
The alarmingly high value is only set to increase, with the European Environmental Agency predicting that global logistics will cause 40% of global carbon emissions come 2050, if no measures are put in place. In working towards achieving the SDGs set by the UN, automation might not be the first ally many in the logistics sector would think of when “going green”.
The Misconception of Automation
Big, power-hungry industrial robots are what most would associate industrial automation with. Those robots unsurprisingly consume loads of energy, thus not aiding the logistics sector with achieving their SDGs. However, recent developments in automation have allowed for sustainable solutions to be used within the sector.
Take AutoStore’s R5 robot for example. These little robots are busy workers aiding human workers with storage and retrieval within warehouses. Despite this, ten of these robots use approximately the same amount of energy as a single vacuum cleaner operating for the same amount of time.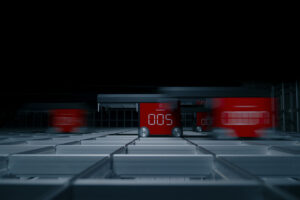
Other innovations within the space allow these robots to not only recharge themselves at the right time to avoid excessive charging, but also have regenerative energy functions to recharge their batteries whenever they store/retrieve or reduce speed.
In totality, they only consume 100 Watts of energy during operation, allowing businesses within the logistics sector to reduce their carbon footprint and fight against climate change.
The Little Things that Add Up
In a traditional warehouse, multiple cogs in its machine are often overlooked when calculating power. Firstly, lighting and air conditioning are two energy hungry aspects of a warehouse. When viewed as individuals within a small area, the consumption of energy efficient bulbs and air conditions might not jump out, but taking into account the sheer size of a warehouse multiplies the amount significantly.
According to Meteor Space, heating and lighting account for over three quarters of total energy consumption. In air-conditioned warehouses, cooling alone takes up 14% of electrical energy in a non-refrigerated warehouse.
In warehouses without automation, forklifts are an everyday essential. With that, these diesel-powered vehicles produce a significant amount of CO2 emissions during diesel production to power the engine, as well as during internal combustion.
Emissions for diesel production are about 500-600 grams of CO2-equivalent per litre. A 2.5t diesel forklift consumes roughly 2-3 litres per hour, resulting in 1,000-1,800 grams of well-to-tank CO2 emissions per hour.
When burning the diesel, it emits approximately 2,640 grams of CO2 per litre, leading to 5,280-7,920 grams of CO2 emissions per hour from combustion.
Automated Storage and Retrieval for a Greener Warehouse
Derived from stacking storage bins one on top of the other in a super-tight storage configuration known as the Grid, an AutoStore Automated Storage and Retrieval System maximises the space of a warehouse. In this system, the R5 robots travel on top of the Grid to retrieve storage Bins and deliver them to workers manning the system’s workstation.
The system promotes collaboration between man and machine within a sustainable and scalable package. Aimed not only to better the lives of workers within a warehouse, the system has wider societal purpose by allowing logistical companies to use this as part of their sustainability and environmental goals strategies.
By utilising the system, it does away with the need of a sprawling power hungry warehouse as the storage configuration allows for 4 times the amount of inventory within the same footprint.
A smaller warehouse means less energy consumed on lights, air-conditioning, and heating. Diesel hungry forklifts are also out of the equation, replaced by eco-friendly robots. These robots can also operate in the dark, allowing warehouses to continue 24/7 operations without using energy for lighting while maintaining operational efficiency.
The Future of Automation in Sustainable Development
Despite the challenges faced in combatting climate change, the future of logistical automation in sustainable development looks promising. As technology continues to advance, these systems are becoming more affordable, easier to program, and more adaptable to different tasks.
With increased collaboration between industry, academia, and policymakers, automation can play a pivotal role in achieving sustainable development goals within the logistics sector.
Eco-friendly robotics are revolutionising industries and paving the way for sustainable development goals. From clean energy production to affordable and sustainable manufacturing, they are contributing to increased efficiency, reduced waste, and optimised resource utilisation.
By harnessing the power of robotics technology, the industry can hopefully create a more sustainable and environmentally friendly future by 2030, and for generations to come. |