How can we make machining sustainable?
The changes that cut waste and increase productivity
Here Emrah Titiz, president of sales, India, at global leader in metal cutting tools Sandvik Coromant, looks at how the machining industry can become more sustainable.
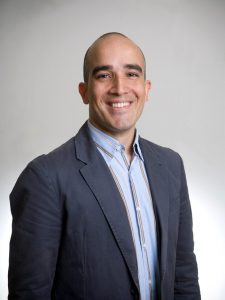
Like many other manufacturing sectors, the machining industry is under rising pressure to develop more environmentally friendly practices. This is in line with Goal 12 of the United Nations (UN) Sustainable Development Goals (SDGs), sustainable consumption and production.
Fortunately, making machining more sustainable doesn’t have to entail high costs and productivity sacrifices. In fact, thoughtful adjustments to processes can simultaneously improve a business’s bottom line and decrease its environmental impact by reducing waste and increasing efficiency.
Reduce tool waste
Tools can be a high source of waste in machining centres. Many tools contain valuable, finite materials, and it’s important that these are kept in circulation to preserve resources. Once a tool has been worn, it doesn’t have to become destined for landfill. The first step to consider in bringing new life to old tools is reconditioning.
In contrast to tool repair, which only fixes the defective part, tool reconditioning rejuvenates the entire tool to bring it back to its original manufacturing standard. With each aspect restored, the reconditioned tool can perform to the same high ability as upon initial purchase. Reconditioning can add multiple use cycles to a tool, therefore reducing the required frequency of replacements.
Manufacturers can maximise reconditioning by considering it from the purchasing stage, through selecting tools that have been designed for multiple reconditioning cycles. For instance, the Sandvik Coromant CoroDrill® 860 with -GM geometry, a solid carbide tool designed for fast and problem free drilling, has been proven to withstand three tool reconditions, substantially elongating its use.
Beyond reconditioning, manufacturers should consider tool recycling as the next step to reduce waste. It’s important that carbide in particular, which makes up around 80 to 90% of all cutting tools, is recycled. As well as cobalt, cemented carbide contains tungsten, which is a rare earth metal with estimated reserves equivalent to around 100 years of consumption.
Recycling tungsten from cutting tools will prolong its natural reserves and allow sustainable use of the material to continue for years to come. As well as saving precious materials, producing tools from recycled carbide emits 40% less CO2 and requires 70% less energy than manufacturing from raw materials.
Sandvik Coromant customers around the globe can benefit from its in house recycling process at its Chiplun site, India. After customer tools are collected and transported to site, they are crushed into a powder that is chemically purified to retrieve valuable materials. Recovered carbide is used to manufacture new tools, and any cobalt is sent to a third party for recycling.
Embrace Industry 4.0
Sandvik Coromant continues its commitment to recycling in its other sites such as Gimo in Sweden, where all tools used in production are recycled after use. Gimo is recognised by the World Economic Forum (WEF) as part of its global lighthouse network, which is a group of manufacturing facilities highlighted as pioneers in adopting Industry 4.0 technologies.
The Gimo tool production plant reaps environmental and operational benefits from its highly automated and digitally-connected systems.
A digital thread runs through the entire facility, containing control systems and sensors that collect valuable data from machines and processes. This information can then be analysed to reveal potential efficiency improvements. Also praised at the site are the fully automated cells with ultra-flexible robots, which allow touchless changeovers during unmanned nightshifts that save time and resources.
In its recent whitepaper, Global Lighthouse Network: Reimagining Operations for Growth, the WEF states that over half the lighthouses in the network are improving sustainability through Industry 4.0 technologies. The document emphasises that sustainability and productivity are intertwined, with digital technologies often improving both simultaneously.
Adopting digital technologies can provide a multifaceted solution to reaching sustainability targets. For example, human errors in programming, using the wrong tools and undetected variations in the raw material can cause unpredictable machining issues that lead to increased scrap. Digital programmes, such as the Sandvik Coromant CoroPlus®, can overcome these issues to ensure the machining task is done in the most optimal way.
The reduction in CO2 emissions from industry in India during 2020 shows the potential the sector possesses to help the country combat climate change.
The machining industry can leverage digital technologies and tool recycling and reconditioning to boost efficiency and cut waste. By adapting processes to minimise their environmental impact, manufacturers can make machining sustainable while also bettering the business.
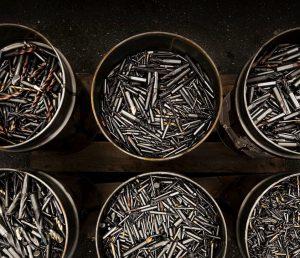