Konecranes CraneQ Geometric Survey assists overhead cranes maximise uptime and safety
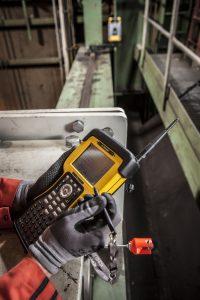
Overhead cranes are workhorses of industry, lifting, shifting and moving heavy items around the clock. If the cranes stop, industry stops, so uptime is vital.
Cranes that are straight, square and aligned properly experience lower repair costs, optimum safety and superior levels of uptime and performance.
To keep cranes on the straight and narrow, global cranes and lifting authority, Konecranes, is introducing its latest CraneQ Crane Geometric Survey, which accurately measures dimensional tolerances of wheels, end trucks, girders, and other components of the crane.
“If cranes are wearing prematurely, positioning incorrectly, or making uncommon sounds, it’s often an alignment issue that’s causing the unnecessary wear on components,” says Mr Nishant Iyer, Consultation Service Manager (SEA), MHE-Demag Pte Ltd (a member of the Konecranes Group).
“A Konecranes CraneQ Crane Geometric Survey helps to find the root cause of any symptoms, to avoid major problems and costly downtime,” he says.
“CraneQ is applicable to all kinds of overhead cranes and particularly relevant to those in heavy duty industries such as steel, paper, manufacturing and mining, where cranes are subjected to harsher operating conditions and more demanding uses.”
CraneQ is based on advanced surveying methods developed specifically for crane geometry. Proprietary software and skilled survey technicians provide an extremely accurate geometric analysis of the crane.
In addition to the survey results, to help plan the best corrective actions, Konecranes shares its expertise and provides advice as the world’s leading crane service organisation, with more than 600,000 pieces of lifting equipment of all makes and models under service contract worldwide.
“CraneQ forms an ideal part of a preventative maintenance programme, because it can identify problems early on. Even if a crane is still operating well, a slight misalignment can cause component parts to wear prematurely, meaning the crane may not perform to its expected design life,” said Mr Iyer.
CraneQ inspections go to the heart of crane alignment
“In terms of a crane’s geometry, it’s the wheels and guide rollers that drive a crane. CraneQ analyses these carefully and provides a detailed report of the crane’s current alignment,” says Mr Iyer.
When performing the inspection, technicians look for key indicators such as:
- Abnormal or premature wear or failure of structural components such as wheels, rails, connections, bearings and guide rolls
- Excessive noise
- Suspected skewing and/or square issues
- Structural deformation
- Positioning, moving and driving issues
CraneQ can be coupled with Konecranes’ other consultation services such as RopeQ magnetic rope inspection and RailQ crane runway survey to give a complete look at the condition and alignment of all elements of a crane.
Key advantages of CraneQ
- Identifies geometric problems that may lead to failures.
- Proven measurement techniques and analysis from a single source.
- Reliable reporting and deeper analysis with accurate results.
- Easier decision making and planning for maintenance and repairs.
- Cost savings when used for preventative maintenance actions.