Life-Changing medical device with Stratasys additive manufacturing
Bluefrog Design, originally named 3CD, was founded in 1990 by Chris Samwell. With 30 years of combined experience as industrial design consultants, the small but expert team at Bluefrog is nothing if not versatile.
Bluefrog serves a wide range of industries including consumer goods, packaging, transportation and medical. Although their clients’ specialities are very diverse, they all look to Bluefrog for innovation.
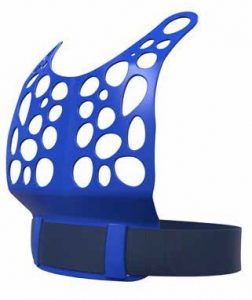
Bluefrog needed the freedom to escape traditional design constraints at every stage of product development. One that could produce fully functional, advanced prototypes with industry-recognized, engineering-grade materials. In a quest to find a solution, the team turned to additive manufacturing.
Overcoming complexities
Bluefrog’s versatility is best exemplified by their ability to find solutions to seemingly insurmountable challenges.
The team was recently approached by a young man suffering from paraesthesia, a condition that causes inexplicable burning, tingling or prickling sensation across the skin. For this patient, the only way to ease his pain was to ensure that his clothes touched his skin as little as possible. Despite interventions from doctors, no solution had been found.
But it was clear to Samwell the patient could benefit greatly from a custom device he could wear with minimal skin contact that would also minimize his skin contact with his clothing. The device had to be customized to his body, resting only on the areas that were not affected by his condition.
Bluefrog Design’s team knew this complex case required a realistic prototype and final product in as little time as possible. They began by creating a complex 3D scan of the patient’s body, which was converted into a 3D printed prototype on their FDM 3D printer.
Once tested and modified, the final version was produced in the tough, medical-grade ABSPlus material, chosen thanks to its advanced material stability over time.
Notably, due to the round-the-clock capability of the Fortus 3D printer, this process took just three days, a dramatic turnaround for a patient who had been suffering for years.
Lightweight, innovative breakthroughs
Thanks to the complex 3D scan of the patient’s body, the team was able to isolate the areas of the patient’s chest that were not affected by paraesthesia, in order to determine where on the body the device could be hung.
Given that the device would need to be worn every day, they also needed to consider its exact weight and shape. It needed to be organic, easy-to-wear and completely personalized.
Stratasys additive manufacturing offered the ability to create a lattice-based design with minimal fuss. They were able to reduce the weight of the device even further and save up to 60% of the material that traditional production methods would consume.
From testing through to the final part, Stratasys additive manufacturing enabled control to optimise the design. They would not have been able to create such a high-performing, unique solution without it.
.
www.objective3d.com.au