Does hybrid manufacturing offer the best of both worlds?
In the wild, zebra and ostriches may appear to be unlikely allies. Here, John Young, country manager for the APAC region at industrial equipment supplier, EU Automation, explains how sometimes a seemingly polarising combination can be very effective, particularly in the realm of additive and subtractive machining.
While zebra have excellent eyesight and a poor sense of smell, ostriches have weak eyesight and a much better sense of smell. By working together, they have a greater chance at identifying threats and evading predators. In much the same way, additive and subtractive manufacturing may seem like competitors, but by combining them, it is possible to overcome their respective deficiencies.
The additive manufacturing market is growing exponentially, and Asia-Pacific is expected to be at the forefront of this multi-billion-dollar market. Japan, China, Australia, and South Korea are among the key global players, while countries such as Singapore are seeing increased government funding in this area.
Despite additive manufacturing being widely heralded as revolutionary, it does have its own set of drawbacks to contend with. Does hybrid manufacturing offer a solution, and could it have even greater potential than its predecessors?
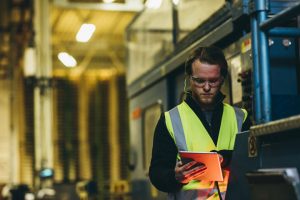
Additive manufacturing, or 3D printing as it is commonly referred to, denotes the production of a part by adding, or “printing”, layers of a material on top of one another.
Additive manufacturing results in less waste material, lighter and more complex designs, and reduced lead times, ideal for rapid prototyping. However, there are drawbacks too; the printing process takes a long time, and finished parts often have an uneven, stepped surface.
Subtractive manufacturing, on the other hand, means creating a product by gradually removing material using techniques including drilling, cutting, and grinding. This method is precise, has a high productivity, and can achieve a range of surface finishes. However, it results in a large amount of waste material.
Hybrid manufacturing combines these two methods. Additive and subtractive manufacturing have been used within the same process for some time, such as using CNC machining to smooth the surface of a 3D-printed product.
However, the term hybrid manufacturing only applies when these different techniques occur within the same machine. These next generation machines may look like a five-axis mill on first glance, but contain a built-in cladding head to carry out additive machining.
Therefore, hybrid manufacturing makes it possible to alternate the two processes. A proportion of a part can be printed, the internal surfaces and features finished with subtractive tooling, followed by the printing of the rest of the part.
Additive manufacturing’s limited accuracy and surface finish are accounted with this combination of methods, as milling is brought back into the process after additive manufacturing, ensuring a high-quality surface finish.
Another benefit is reducing waste by adding only the amount of material necessary before tooling, maximising the efficiency of any machining work needed, and dramatically reducing costs. Hybrid technologies can be used to build up and repair damaged parts, or to combine different materials, such as copper for heat transfer.
While 3D printing was once ubiquitous with polymers, hybrid machines can use combine a range of metals and alloys to create a single product, using more costly materials only where required.
Hybrid CNC machines are expensive, but as only one machine is needed for the full production cycle, they could reduce overall capital equipment costs in one compact footprint. They also minimise the risk of error, as there is no need to move a printed part to reset it on a separate machine.
Applications of this technology are diverse, but it is expected to make an impact on the medical, automotive, electrical, aerospace, industrial systems, and consumer goods sectors, amongst others.
Just as the zebra and ostrich alliance is a match, so too is the additive and subtractive manufacturing combination. While it is yet to reach its peak, new technologies and applications are continually being discovered for hybrid manufacturing.
It will offer businesses in Asia-Pacific the best of both worlds, enabling them to make the most of the unrealised potential promised by additive manufacturing.