Manufacturing in 2020
How does your company see the year ahead? We’re using our crystal ball here and invite you to do the same. Tell us how you see things and developments you are looking forward to. – ed.
Manufacturing in 2020 will be exciting, dynamic, and competitive.
With the emergence of billions of new consumers into the “developed” world, the emphasis on education, the pressure to raise or maintain living standards while consuming fewer resources, and the global availability of knowledge, manufacturers will have unprecedented market opportunities.
The development of adaptive, reconfigurable equipment, processes, and systems will enable the rapid reconfiguration of enterprises to meet competitive pressures but will also improve the integration of human and technology resources, enterprise-wide concurrency, and the development of revolutionary processes.
Second, research on modelling and simulation will help meet the challenges for enterprise-wide concurrency, the utilisation of human and technological resources, the conversion of information to knowledge, and the rapid reconfiguration of manufacturing enterprises.
Finally, research on information technology will help to meet all the grand challenges. Information technology is the primary technology for converting information to knowledge and will be a key technology for concurrency, the integration of human and technical resources, and the rapid reconfiguration of enterprises.
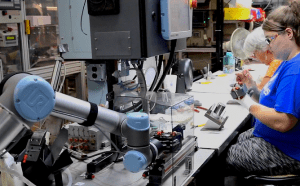
Recommendation. Establish priorities for long-term research with an emphasis on crosscutting technologies, i.e., technologies that address more than one grand challenge. Adaptable and reconfigurable manufacturing systems, information and communication technologies, and modelling and simulation are three research areas that address several grand challenges.
Breakthrough Research
Technological breakthroughs in two areas—innovative submicron manufacturing processes and enterprise modelling and simulation—would have a profound impact on manufacturing of the future.Bottom of Form
Submicron Manufacturing
Submicron manufacturing promises to provide economic solutions to meeting increasingly demanding customer needs and, at the same time, decreasing time to market, energy consumption, and environmental costs.
Manufacturing at the submicron level has four important aspects—evolutionary advances in (1) miniaturisation and (2) microelectromechanical systems (MEMS), as well as revolutionary advances in (3) nanofabrication and (4) biotechnology.
There has been a steady trend toward miniaturising manufactured components. A good example is the progression from vacuum tubes and discrete transistors to the very dense integrated circuits manufactured today.
Integrated circuits contain structures, produced in layers using photolithographic processes, with features on the order of a micron or less in size.
For compelling economic reasons, the semiconductor industry continues to reduce the dimensions of integrated circuits.
The proliferation of more and more powerful, but smaller and smaller, intelligent systems will lead to advances that will be crucial for meeting several of the grand challenges for manufacturing in 2020.
MEMS use sensors, actuators, and other electromechanical structures with dimensions on the order of microns.
Like integrated circuits, MEMS are produced using the batch-processing capabilities of semiconductor processing.
In fact, MEMS can be part of integrated circuits that combine machine intelligence with electromechanical action.
The ultimate in submicron manufacturing is nanofabrication, specifically molecular nanotechnology (MNT), in which individual atoms and molecules are manipulated to form materials and structures.
The consensus among MNT researchers is that, in principle, a wide range of molecular structures can be produced cost effectively.
MNT could enable the production of new materials with specific properties tailored for given applications, properties that could be varied as structures are built up to produce functionally gradient materials.
In addition, materials and structures with dramatically improved properties could be produced with no waste. Costs for self-replicating materials manufactured by MNT could be reduced to competitive levels by 2020.
If costs are competitive, MNT will have far-reaching implications for waste-free manufacturing of very light weight, strong microstructures and macrostructures.
One important form of self-replication at the molecular level that occurs naturally is controlled by DNA and cellular processes.
Biotechnology has already progressed to the point that genes can be manipulated. By 2020, a substantial technology will have been developed to produce biological materials, the replication of biological materials, and the formation of structures from biological materials.
The interrelationship between bioprocessing and MNT could lead to the production of hybrid structures that combine DNA and machine intelligence with biological and nonbiological materials.Bottom of Form
Modelling and Simulation of Manufacturing Systems
Meeting the grand challenges of concurrency in all operations (grand challenge 1) and rapid reconfiguration of manufacturing enterprises (grand challenge 5)—which include enterprise strategy, planning, and operations at one extreme and manufacturing cell operations at the other—will depend on accurate predictions and timely decisions based on modelling and simulation to develop virtual prototypes.
Manufacturing systems in 2020 will be complicated, dynamic amalgams of human and machine intelligence, knowledge, materials, equipment, and processes. Operational decisions made at relatively low levels in the enterprise may have enterprise-wide consequences.
Two crucial elements are necessary for successful manufacturing systems models and simulations—a comprehensive set of models and human-machine interfaces that enable individuals to interact with the models for learning, planning, and manufacturing control.
The semantics of manufacturing that encompasses all enterprise operations and functions within a globally distributed real (or virtual) manufacturing enterprise must be consistent across all levels, operations, and functions of the enterprise.
Ideally, the semantics would support global multi-objective optimisation of the enterprise and its operations; that is, it would be robust enough to be the basis for a theory of manufacturing and adaptable enough to support change.
Individuals will be critical components of any manufacturing system. Models and simulations must account for individuals from two points of view.
First, the behaviour and actions of individuals, as part of a manufacturing system, must be included in the models.
This implies an understanding of how individuals relate to each other within the system, as well as an understanding of how individuals relate to equipment and processes (which may or may not be automated).
Second, models and simulations must be described and delivered in a usable form to facilitate the decision or action that must be taken.
Including human behaviour, with all its vagaries of learning and communication styles and overtones of culture and language, will make modelling and simulation difficult. However, unless the human factor is included, the representation will be unrealistic.
Recommendation. Establish basic research focused on breakthrough technologies, including innovative submicron manufacturing processes and enterprise modelling and simulation.
Focus basic research on the development of a scientific base for production processes and systems that support new generations of innovative products.
Taking Advantage of “Driver” Technologies
Some of the technology areas for meeting the grand challenges are being developed for other purposes.
For example, information is a core technology thatBottom of Form
is applicable to grand challenges for concurrency in all operations (grand challenge 1), integration of human and technical resources (grand challenge 2), transformation of information into knowledge (grand challenge 3), and rapid reconfiguration of manufacturing enterprises (grand challenge 5).
Information technologies that enable seamless, collaborative systems may not be useful for manufacturing without a further determination of how people, machines, and information technology can work together beneficially in manufacturing systems.