Composites for car part manufacturing
The US Environmental Protection Agency (EPA) mandated in 2012 that the national automobile fleet should average 54.5 miles per gallon by 2025 in order to reduce reliance on fossil fuel and minimize emissions, many other nations have also implemented similar new standards.
To meet these new standards the automotive industry has had to find new ways to make lighter cars without sacrificing their strength and structural integrity.
Here Jari Sopanen, Regional Manager at leading composites manufacturer Exel composites explains why one of the best replacements for steel is thermoset components.
Thermoset composites are formed using glass, carbon, or aramid fibres, which are then combined with resins such as polyesters, vinyl esters, epoxies, or phenolic resins.
These composites are used in various industries but are particularly prominent in the manufacturing of aircraft and spacecraft parts.
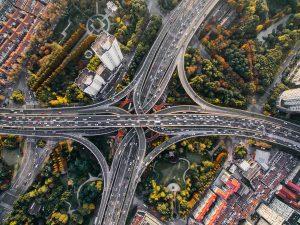
Thanks to research and development in the aerospace sector, composites are also being used across other forms of transportation due to the high demand for lightweight vehicles and components. This trend, called light-weighting, seeks to use innovative materials to reduce the weight of products.
As a result, composite materials are being increasingly used in production, especially for automotive parts and components.
According to the American Composites Manufacturers Associations, fiberglass is one of the key reinforcing materials used in the US thermoset composites industry.
Thanks to its durable properties, it is a good replacement for steel in vehicle structural components, including drive shafts, bumpers and roof beams
Reducing component weight is crucial for raising the efficiency of automotive systems. For example, carbon fibre has comparable properties to steel, but is only one-fifth the weight.
Regardless of the mode of transport, it is easy to see the benefits that shaving this amount of weight from a vehicle will achieve.
Additionally, when directly compared to steel, composite materials can meet or surpass the automotive industry’s material property demands, including low coefficients of thermal expansion for heat conduction, dimensional stability for shape retention, corrosion resistance in wet conditions, and high-impact strength to withstand repeated use.
The low weight of composite components also helps provide good sound baffling and an overall quieter performance.
One type of car that can massively benefit from composite components are electric vehicles (EVs). Batteries are heavy and, although technology is advancing at a blistering pace, it is highly likely that the bulk battery weight will not decrease as any miniaturisation will be used to install more batteries to increase range and power.
Minimising component weight is, therefore, critical and fibre glass and carbon fibre alternatives are incredibly suitable for this light weighting, especially for EVs.
For example, EV batteries must be held in special boxes to protect them but also to prevent any discharge from shocking passengers.
Metals are conductive, which makes them unsuitable whereas most composites aren’t, meaning that when made from composites, which possess a higher strength to weight ratio, they are perfect for this application.
Due to EVs current limited distance range, shaving off weight can produce strong marginal gains.
Composites are gearing up to feature in more than just structural components for cars. In fact, many Asian countries are increasing their composite production, because composite materials are becoming increasingly popular in their electronics sector, especially with companies supplying to the automotive sector.
While North America and Europe account for a key share of the global thermoset composites market, which is expanding due to the local automotive and aerospace industries in these regions, an increase in demand for electric and lightweight vehicles is also anticipated to propel the composites market in the Asia Pacific region and beyond.
With governments across the globe looking to implement more rigid energy efficiency standards, shedding vehicle weight is an achievable objective that can help car manufacturers to meet regulations.
Composites material developments means that now they are much better suited to automotive applications in comparison to steel and it is time for car manufacturers to start considering the material as a viable solution.
.