The four factors essential to building a quality production line
-Andrew Stackpole, Assembly Shop Manager at Facteon
Developing an efficient and polished machine building process can take a manufacturing company decades.
What’s most important is that throughout this process, the focus is on building a quality production line that allows for the manufacturing of best-in-class product.
Since beginning my career as a Machine Builder in 1994 and working through to my current role as Assembly Shop Manager at Facteon, I’ve come to learn that there are four key factors involved in developing a quality production line.
1. Quality components produce quality product
By keeping the production of machinery components in-house where practical and possible, you will play a more active role in quality control.
It was for this very reason that Facteon established its own in-house Build Shop and Machine Shop to cater to internal and external customers. The team retains full control over every component produced and as it’s not heavily relying on delivery by third parties, it can be certain that the component will be available on site when required.
To achieve the necessary levels of precision in component manufacturing, collaboration is key – both in the initial phase of producing your components and in the build phase of the production line.
Looking at opportunities to integrate the latest technologies with more traditional machining methods, will allow you to fully harness the potential of the machinery while using the latest technology to improve precision and efficiencies.
- Partnering with reliable external suppliers
For any components that can’t be produced in-house, consider looking beyond your own capabilities and using the services of thoroughly vetted external providers.
For example, Facteon uses suppliers based in New Zealand, China and the United States and vets these suppliers through a tiered rating system to ensure that our standards are met.
If you’ve outsourced the production of a component, it’s wise to have an experienced machinist inspect it when it’s delivered to ensure it meets your own standards, before it is moved to the component bin for inclusion in the production line.
Success here will depend on how closely you can work with external suppliers prior to and during the manufacturing process. A quality deliverable is only achievable if your standards are communicated and understood by the supplier.
To negate the potential for errors in components manufactured externally, building strong relationships with external providers is key. It’s vital that the supplier understands how the component will integrate with the project as a whole.
This allows the machinists to raise any concerns and share ideas while also increasing motivation levels as the component contributes to the success of the production line.
This approach can also be effective when it comes to internal machining as well.
3. Invest in developing quality people to build quality lines
Employing the latest machinery is pointless without skilled operators. Exposure to all stages of the machine building process allows for greater understanding, and ultimately, an improved quality of work.
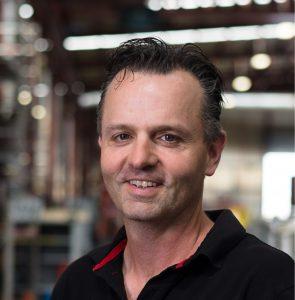
As I’ve mentioned above, during the machine building phase it’s important that there’s coordination between machine builders and design engineers. In my experience, I’ve found that positioning the design engineers in the facility where the lines are built allows for greater consultation throughout the build process.
It’s also worth thinking about how your Build Shop staff can learn from their colleagues, including the project managers and design engineers, to better understand the projects they’re working on. This delivers value to your customers, as staff with varied skill sets can work collectively to maximise the potential of the production line.
This collaboration should also be complemented by extensive in-house training at all levels. For example, if you have several senior machine builders on-site, there are many learning opportunities for apprentices and intermediate-level machine builders.
Providing staff with the opportunity to spend time on customer sites prior to on-site commissioning can also boost integral client service development skills. Not only do they gain a greater understanding of the customer’s needs throughout the design, building and commissioning process, but this high level of integration also ensures a higher quality of work as they learn to recognise the impact each smaller part has on the project as a whole.
4. Quality project management to ensure successful delivery
Ensuring the seamless transition from the production line building stage to the delivery of the line is a key responsibility of an Assembly Shop Manager.
This includes working closely with the customer’s dedicated project manager – their key point of contact and advocate within the business – throughout the machine building process.
In my experience, project managers who frequently spend extended periods of time on customer sites during the installation and commissioning phases, are better able to facilitate the process of integrating a production line into an existing factory.
As part of this integration process, I recommend offering training to the customer’s team to ensure it understands how to safely and effectively operate the production line post-installation. This induction process is essential in enabling factories to produce quality product once the line is up and running.
The team must also be adequately prepared to provide ongoing support to the customer. This is integral to the longevity of both the customer relationship and the production line itself.
If producing quality products is at the core of your customers’ operations, developing a machine building process that delivers on this key requirement is paramount.
Ultimately, the intersection of quality components produced both in-house and by top-tier external suppliers, coupled with expert staff and a strong project management offering, will allow any manufacturer to continue delivering quality production lines on-time and to specification.