The promise of the edge and IIoT in Asia’s manufacturing industry
To remain competitive in today’s always-on world, organisations require near-instant access to data and resources. That’s where the edge comes into play: the place where computing occurs, in between the data centre and the cloud.
In Singapore and Asia, edge computing poses a great opportunity to enable improved real-time decision-making – especially in Asia’s booming manufacturing sector. In a rapidly growing industry, the Industrial Internet of Things (IIoT) is lighting the way for a highly automated future.
The IIoT refers to a combination of intelligent computers and devices that enable instant data sharing and automated processes in industrial manufacturing. The IIoT is set to revolutionise manufacturing by providing accessibility to large amounts of data at far greater speeds.
According to a report by Boston Consulting Group, Five Profiles That Explain China’s Consumer Economy, GDP growth in China, the world’s second largest economy, has slowed from more than 10% in 2010 to around 7% in 2017.
To remain competitive, Asian economies – once reliant upon low-cost labour and exports – are under pressure to adopt smarter technologies, such as robotics and the IIoT. Going forward, it is predicted that smart technologies and IIoT networks will allow industrial organisations to break open data silos and connect people, data and processes like never before, from the factory floor to executive offices.
Automation and the future of manufacturing – So where does edge computing fit into all of this?
The promise of edge computing in industrial environments means switching into the right device in near real-time to drive faster decision making. For this to work, the edge device and its embedded software, edge servers, gateways and cloud infrastructure must be up-and-running correctly at all times.
According to a recent report by ARC Advisory Group, Is IIot Living on The Edge In Industrial Environments? forward-thinking organisations are implementing edge infrastructure to optimise performance and production outcomes.
The report surveyed a group of over 300 end-users across the globe to assess the state of play in the market. Key findings from the report include the fact that over half of industry leaders are planning to invest in the edge and the cloud to create more robust infrastructure and enhance automation.
The majority of leaders agree that deploying real-time data analytics will improve asset performance and maintenance, optimising production and preventing unplanned downtime. At the same time, edge analytics have the power to significantly reduce dependency on human effort, improving operational efficiencies and reducing manual labour costs.
How does edge computing benefit the end-user?
ARC Advisory Group’s report found that the top three benefits for deploying systems and connectivity at the edge are operational: analysing and controlling devices, improving process speed/reducing latency issues, and reducing data security risks.
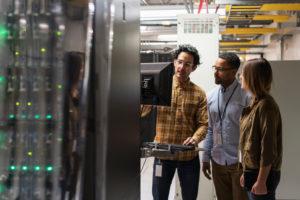
The decision to implement an edge computing architecture is typically driven by the need for location optimisation, security, and most of all, speed. Edge computing provides this by pushing applications, data and computing power services away from centralised data centres to the logical extremes of a network, close to users, devices and sensors.
In this way, edge computing enables companies to put the right data in the right place at the right time, supporting fast and secure access. The result is an enhanced user experience and a strategic advantage in today’s increasingly competitive manufacturing industry.
Edge computing and analytics are increasingly being located close to the machines and data sources. As the digitisation of industrial systems continues, so does analysis, decision-making and control being physically distributed among edge devices, edge servers, the network, the cloud and connected systems.
Building the interconnected systems of the future
Innovative IIoT and edge devices are building the interconnected systems of the future. However, across factory ecosystems, products, equipment in the field and the manufacturing supply chains, these devices and connections must be made secure and reliable, or manufacturers will slow down the deployment of edge and cloud innovations.
In the very near future, companies will be leverage data to identify production inefficiencies, compare product quality against manufacturing conditions and pinpoint potential safety, production and environmental issues. Remote management of edge infrastructure will immediately connect operators with off-site experts to be able to avoid or more quickly troubleshoot and resolve downtime events.
The growth of IIoT in Asia extends the edge to industrial devices, machines, controllers and sensors. Going forward, smart manufacturing and edge computing with information-enabled operations offers virtually infinite potential to improve business performance.
The Stratus solution
Stratus’ edge solutions begin with ftServer, the ideal system for digital transformation initiatives at distributed enterprises. An intelligent, self-monitoring, self-diagnosing, self-healing computer system, ftServer is best suited for remote hybrid deployments or customers within process manufacturing, where fault tolerance is business-critical.
The latest version of ftServer brings VMware support along with better performance, enhanced availability and improved manageability. These improvements help customers and partners accelerate time-to-value, maximise revenues and increase efficiency.
“The more automated and connected applications become, the more critical it is for customers to have a highly reliable, continuously available and operationally simple edge infrastructure to drive true IIoT business value.”